Source: renewableenergyworld.com
Published: October 12, 2012
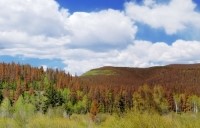
Lead image: Pine beetle damage via Shutterstock
SEATTLE — At least one University of Washington chemical engineer is working on a thermo-chemical conversion technology that should make renewable energy “lemonade” from a particularly problematic batch of biomass “lemons.”
Armed with a $200,000 U.S.D.A. two-year research grant, Fernando Resende will start work on a fast pyrolysis mobile reactor next year that could revolutionize how foresters and the timber industry currently deals with millions of acres of Mountain Pine Beetle-killed softwood trees.
The goal is not only to produce an economically-viable new source of renewable liquid bio-fuel targeted for use as bio-diesel or aviation biojet, but to mitigate forest fires and beetle infestations in Lodgepole and Ponderosa pines over large swaths of the Pacific Northwest and the Intermountain West.
Climate change and moratoriums on logging in the 1990s are thought to have only exacerbated the infestations which normally reappear every forty years or so. The most recent pine beetle epidemics appear to have peaked within the last five years, and though their tree kills will create problems, they will also create potential renewable energy biomass feedstocks for another couple of decades.
“The idea is to use fast pyrolysis to take wood particles and decompose [their] large long molecules of cellulose or lignin into liquid bio-oil,” said Resende, an assistant professor in the School of Environmental and Forest Sciences at the University of Washington in Seattle. “We would use a thermo-chemical process instead of a bio-chemical process with mobile pyrolysis reactor units about the size of a large flatbed truck.”
Pyrolysis thermally decomposes organic matter to produce carbon monoxide, hydrogen, and methane; solid char; and liquid bio-oil. While slow pyrolysis has long been used to produce charcoal, fast pyrolysis is a state of the art technology that can heat biomass to 600 degrees Celsius in a little over a second, then cool it just as rapidly. For beetle kill tree conversion, fast pyrolysis is expected to produce at least 70 gallons of bio-oil per ton of wood.
When heated, says Resende, the wood is converted to pyrolysis vapors that flow into a condenser, where they are flash-cooled by exchanging heat with a stream of cold water and ethylene glycol. Then once these vapors cool, what’s left is liquid bio-oil.
Although such pyrolysis promises high bio-oil yields, the whole process would require fairly extensive onsite prepping.
The pine beetle kill biomass would first have to be logged, milled and dried into particles that would enable its fast pyrolysis. Then once the wood had been converted to bio-oil, it would still need off-site refining to ready it for a commercial transport market.
And, in principle, there would hardly be a shortage of biomass. Infested trees are prevalent throughout South Dakota, the Intermountain West, British Columbia, Oregon, Idaho, Washington, Colorado — even parts of New Mexico. In fact, David Shaw, a forest health specialist with Oregon State University Extension Service in Corvallis, says that, likely due to warmer temperatures, the size of the epidemic is now at the northern limits of the beetle’s range.
All this dead timber only fuels already rampant forest fires, creating a hazard for healthy trees, not to mention nearby towns and residential areas throughout the West. Within 15 years after their death, the infected trees lose 90 percent of their moisture. That’s not great for the timber industry but is a potential boon for proponents of beetle kill bio-fuel, because this dead dry wood is more brittle and easier to break down thermo-chemically.
“Once the tree becomes infested, its value drops dramatically,” said John Ball, a forest health specialist at South Dakota State University in Brookings. “We’re left with huge amounts of biomass that can increase fire risk and that no one can use. So, to find a means to convert it to something usable would be incredibly valuable. Even if this technique was limited and fairly expensive, it would still be great.”
Estimates are that beetle kill-fed mobile pyrolysis units will run as much as $4 million each; would process 50 dry tons of wood per day; and produce bio-oil with an energy density that is as much as seven times that of wood chips. However, these mobile units would also enable operators to avert transport costs for low-value beetle-kill biomass.
Current estimates, says Resende, is that some 75 percent of the dry weight of the wood could be converted into biofuel. To make the technique economically viable, Resende plans to convert a minimum of 73 percent of the wood’s dry weight into liquid oil.
One of the technology’s economic wildcards involves just how small the wood particles need to be for processing. For normal fast pyrolysis, Resende says that could vary from a millimeter to some ten millimeters.
“Fast pyrolysis [normally] requires grinding the wood to very small particles which would make it economically unfeasible,” said Resende. “We are proposing ablative pyrolysis, a method [by which] the wood is pressed with a hot metallic surface, so that the heat transfer is done by solid to solid contact. That way, we don’t have to grind the wood to such small particle sizes.”
But Mark Coleman, a forest biologist at the University of Idaho, says that he is confident that when the technology is fully developed, it would at least be competitive with ethanol.
“[In South Dakota], we’re paying $18 a tree to have infested trees cut,” said Ball. “So even if this fast pyrolysis method cost $3 a tree, we still save fifteen bucks a tree.”
Mike Cloughesy, the director of forestry with the Oregon Forest Resources Institute, says such dead trees in his own state are often sited on public lands and inaccessible wilderness areas that can’t be logged.
With Oregon’s strong environmental lobby, however, the challenge could be more political than logistical.
“But, [with beetle kill], just letting nature take its course is probably not wise,” said Ball.